IntelliDapter™ Motorization Technology
Overview
IntelliDapter™ is a small module that instantly motorizes the tilt function of any ordinary wand-operated miniblind.
Unlike most other retrofit tilt-motorization technologies, IntelliDapter™ fits outside the headrail of the host blind, and can be installed without tools and without need to remove or modify the host blind in any way. And unlike some other external motorization technologies, IntelliDapter™ is mounted directly to the host blind's headrail, well above eye level, so it doesn't disrupt the visual continuity of the window.
In addition to a small gearmotor, IntelliDapter™ consists of a headrail-attachment bracket, a shaft coupler that connects the gearmotor's output shaft to the blind's tilt adjustment shaft, and an innovative floating gearmotor mount:
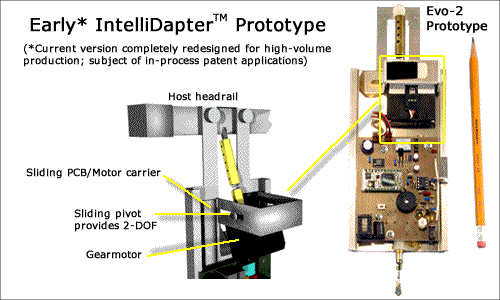
The motor mount provides three degrees of freedom of gearmotor movement—vertical, lateral, and rotary in the prototype shown here—while reacting the torque produced by the gearmotor.
Compatible with Virtually Every Wand-Actuated Miniblind Ever Produced
The IntelliDapter™ gearmotor mount's multiple degrees of freedom allow its output shaft to line up coaxially with the host blind's tilt-adjustment shaft, regardless of the latter's length, orientation, or location relative to the top of the headrail. And the shaft coupler allows IntelliDapter™ to be securely coupled to any blind's tilt-adjustment shaft in just seconds, regardless of its diameter or number of locating holes. These innovations enable IntelliDapter™ to quickly motorize any of the over 500 million wand-actuated miniblinds currently installed in U.S. residential and commercial buildings.
Reduced Component Costs
Generally, the cost of a motorized product depends on factors such as the required torque, speed, quietness, and lifetime of the drivetrain. But with the conventional miniblind motorization products available today, there's another cost driver: the components must fit within the headrail of the host blind.
On the other hand, with IntelliDapter™, a relatively large volume is available for the structural and electromechanical components, and there are no form-factor constraints on the gearmotor. Also, because the gearmotor is coupled to the blind's existing tilter (rather than directly to the blind's internal tilt shaft), the required torque is reduced by the tilter's gear ratio, enabling a simpler, less expensive geartrain.
These factors enable the use of inexpensive stamped and injection-molded parts for the bracket and mount, along with an inexpensive "commodity" gearmotor originally developed for use in toys and cordless appliances. As a result, IntelliDapter™ has a component cost that's less than 50% of that of currently available miniblind motorization products.
Easier Installation
All of the miniblind motors currently available are designed to be installed within the headrail of the host blind. This isn't a major issue if the motor is installed when the blind is originally assembled, but substantially increases installation labor in a retrofit application:
- The host blind must be removed from the host window in order to gain access to the headrail.
- Typically, the blind's internal tilt shaft must be shortened (i.e. with a hacksaw) to make room for the motor.
- The motor and its control electronics must be inserted.
- The blind must be re-installed to the host window.
On the other hand, with IntelliDapter™, there's no need to remove, modify, or re-install the host blind. That reduces installation labor by more than two-thirds relative to internal motorization products. And the ease of installation makes products based on IntelliDapter™ much more amenable to direct-to-end-user distribution, e.g. for residential DIY applications.
Major Reduction in Net Installed Cost
By reducing motorization component costs and installation labor, IntelliDapter™ motorization reduces the overall costs of miniblind automation by a substantial fraction—even in sophisticated systems that include significant sensor and control functionality beyond motorization.
For example, the following chart provides a retrofit cost breakdown of several automated miniblind systems capable of Dynamic Daylight Control (DDC), i.e. automatically self-adjusting to maintain a desired daylight level under changing conditions. Two systems are shown: the least expensive DDC system based on conventional technology, and several variants of IntelliBlinds™, all of which incorporate IntelliDapter™ motorization:

Thanks to multiple innovations, IntelliBlinds™ has a retrofit cost per window that's just one-third that of the conventional DDC system—and IntelliDapter™ accounts for the greatest portion of those savings, cutting the net retrofit cost by 40%. The percentage savings due to IntelliDapter™ would be even greater for a simpler automated miniblind system without DDC capability.
Intellectual Property Protection
IntelliDapter™ Motorization technology is protected by claims in U.S. patent 5,570,558, with an additional patent application in the process of being filed.
Summary of Key Points
- IntelliDapter™ motorization is a miniblind-motorization technology that attacks the four largest cost drivers of blind-based automated shading in retrofit applications: the motorization components, installation labor, the new blind, and the lost investment in the existing blind
- IntelliDapter™ mounts outside the headrail of the host blind, enabling it to take advantage of low-cost commodity motorization components
- It can be installed in minutes, without tools, and without need to remove, modify, or re-install the host blind
- Thanks to its patented floating motor mount and innovative shaft coupler, it can be used with any of the 500 million shaft-actuated miniblinds already in use, eliminating the cost of a new blind as well as the lost investment in existing blinds
- Even compared to conventional motorization products that can be retrofitted to existing blinds, IntelliDapter™ reduces the costs of miniblind automation by at least 40%. And that's for a complex automated system with sophisticated sensors; the percentage savings are even greater in simpler systems where motorization accounts for a greater fraction of overall product cost